Heavy-Duty Truck Towing Capacity: How Maintenance Affects Performance
Keeping your trucks running smoothly is straightforward. It all comes down to regular maintenance checks, spotting concerns before they escalate, monitoring fleet status, and establishing prevention-focused strategies. Routine checks and fixes guarantee optimal uptime, enhanced performance, and safety. Direction from specialists from experts like Jim enables you to excel in fleet maintenance through the smart implementation of technology, thorough logging, and skilled staff. Start exploring this complete guide to fleet maintenance and open the door to cost-effective operations. There's much to explore and master!
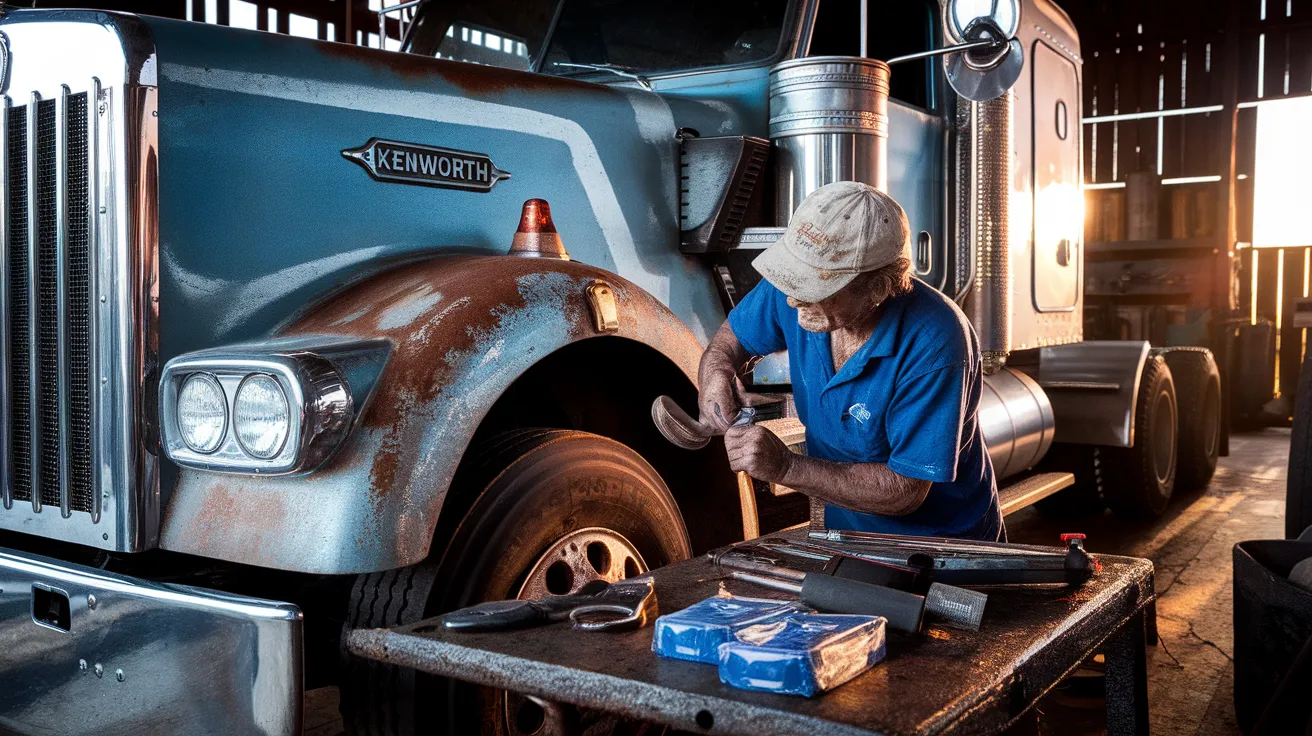
Key Takeaways
Recognizing the Importance of Scheduled Fleet and Truck Service
While it may appear challenging, understanding routine vehicle and fleet upkeep is essential for any successful business. You'll find the advantages of maintenance far outweigh your investment of time and energy. Routine inspections and maintenance can greatly increase your fleet's service life, avoiding hefty replacement costs. Plus, there's an undeniable connection between well-maintained trucks and improved fuel efficiency. This results in reduced gas expenses, boosting your total operational efficiency. Moreover, frequent maintenance can uncover minor concerns before they become serious problems, avoiding expensive repair bills later on. Thus, don't underestimate the power of regular upkeep; it can be a significant factor for your business's bottom line.
Recognizing Critical Aspects of a Effective Maintenance Program
To secure your fleet's efficiency and durability, it's critical to recognize the fundamental aspects of a effective maintenance program. You'll need to understand the basic principles of maintenance, monitor the status of your fleet consistently, and put in place preventive measures ahead of time. With these established, you're positioned to reducing downtime and enhancing productivity.
Essential Program Maintenance Elements
When it comes to enhance your fleet's performance and durability, creating a comprehensive maintenance program is essential. Key components of the program consist of regular inspections, systematic servicing, and anticipatory repairs. Each aspect is instrumental in preventing major malfunctions and reducing downtime. While the benefits of a maintenance program are substantial, you must consider the implementation challenges. These can range from logistical issues and employee pushback. However, with careful preparation, clear communication, and dedication to training, these barriers can be surmounted. Remember that an effective maintenance program isn't just about repairs; it stops them from occurring. It's an commitment in your fleet's longevity – and it's one that will yield significant returns.
Asset Performance Monitoring
When examining the key elements of a successful maintenance program, understanding the critical role of fleet condition monitoring is essential. It goes beyond maintaining operational vehicles, it focuses on maximizing fleet performance. Fleet monitoring systems provide a comprehensive view of your fleet's condition, enabling you to detect potential issues prior to escalation.
These monitoring systems track important indicators like fuel consumption, tire conditions, engine status, and more. By leveraging this data, you're not simply safeguarding the lifespan of your fleet but also reducing avoidable maintenance expenses. Remember proactive identification is essential in fleet management. Thus, adopt trustworthy monitoring technologies and stay ahead of the curve. Avoid simply responding to problems, anticipate them. Maintain your fleet's optimal condition and your operation will run smoothly.
Establishing Preventive Protocols
Although tracking your fleet's condition is crucial, putting preventive strategies in place is just as crucial to maintain a effective maintenance program. You must spot potential problems before they develop into costly repairs or downtime. Let's discuss preventive strategies.
An important measure is establishing a thorough maintenance checklist. This checklist should specify all essential checks, service tasks, and replacements. Routine engine monitoring, tire maintenance, and oil changes are a given. But don't overlook basic components like wipers, illumination, and filters.
Your checklist should also include a timetable for all maintenance tasks. Following this plan makes certain that your fleet maintains optimal performance. Keep in mind, preventative care cuts down on expenses, time, and problems in the future.
Key Maintenance Tasks for Truck and Fleet Maintenance
To guarantee your truck and fleet stay in optimal condition, you should focus on regular maintenance inspections. These checks include scheduled maintenance inspections and key parts inspection. By following these essential protocols, you'll increase your fleet's longevity, optimize operational efficiency, and in the end, save on major repair expenses.
Routine Equipment Inspections
Regular maintenance inspections serve as your best protection against unexpected vehicle and fleet malfunctions. They provide you an opportunity to spot and address concerns before they escalate into serious accidents or expensive repairs. A key scheduled maintenance benefits is the reduction of operational delays, which can substantially influence your company's productivity and bottom line.
Vital Component Assessments
Building on the critical nature of scheduled maintenance inspections, let's explore the key essential component checks that ought to be conducted regularly to maintain optimal truck and fleet performance. Start with the brake system – verify all components are functioning efficiently, from brake pads to fluid levels, while also checking for leaks. When overlooked, brakes may malfunction, leading to catastrophic incidents. Tire pressure checks are equally essential. Low pressure increases fuel consumption and tire wear, while excessive pressure risks a blowout. Purchase a quality pressure gauge for accurate readings. Note that tires should be cold during checks for best results. Consistently conducting these essential checks can save you from costly repairs and potential accidents. Drive safely on the road.
Essential Fleet Maintenance Practices for Peak Performance
While overseeing a fleet, it's crucial that you emphasize preventative maintenance to ensure peak efficiency. Establishing a well-structured preventative scheduling system is key. This prevents unnecessary wear and tear, and lowers the chances of unscheduled downtime. You should schedule regular maintenance and inspections based on time, mileage, fuel consumption, or engine hours. Keep in mind each vehicle is distinct and could require a customized approach.
Training in maintenance is an essential method to ensure peak efficiency. Give your personnel the essential skills to detect potential issues before they escalate. This not only saves time but also lowers operational costs. The combination of preventative scheduling and maintenance training will lead to a more productive and dependable fleet. Remember, an ounce of prevention is worth a pound of cure.
Expert Recommendations for Commercial Vehicle Restoration and Repair
Although fleet and truck maintenance and restoration can seem overwhelming, knowing the basics can help simplify things. Your starting point needs to be to learn about different maintenance methods. This knowledge will enable you to diagnose problems quickly and efficiently. Following this, prioritize maintenance work depending on the severity of damage and the truck's function in your vehicle lineup. Frequently check all units for developing concerns and fix them immediately to avoid additional problems. Remember, restoration isn't just about fixing issues, it's aimed at upgrading the unit's efficiency and durability. Lastly, consistently choose top-grade materials for repairs; they'll last longer and perform better. Follow these principles, and you'll handle truck and fleet repair and restoration with ease.
Leveraging Sector Developments for Cutting-Edge Fleet Maintenance
To remain competitive in the trucking industry, it's crucial to leverage industry innovations for improved fleet maintenance. New technologies are rapidly changing the maintenance landscape. Make use of data analytics to track your fleet's performance and anticipate potential issues in advance.
Modern tracking solutions keep track of engine conditions and status, fuel consumption, and operator performance. Leverage these insights to plan preventive maintenance, minimizing costly operational interruptions.
Don't overlook software updates. They usually provide important fixes and improvements that optimize your automotive fleet's safety and performance. Keep in mind fleet management goes beyond routine maintenance. You're operating in a tech-focused environment, and staying current with sector developments will promote your vehicles' longevity and profitability. Through proper systems, you will decrease costs and time, and help protect lives.
Questions & Answers
What Credentials Do You Need for a Skilled Fleet Maintenance Mechanic?
You will require a valid certification, satisfying the standards of an established mechanic institution. Furthermore, you require a thorough skill assessment, proving your knowledge in multiple facets of fleet service and repair. Experience counts too!
What's the Right Time to Replace Fleet Vehicle Tires?
Similar to clockwork with the changing seasons, you should regularly check your fleet's tire wear regularly. Yet, it's generally recommended to replace tires every three to 6 years, based on road conditions and usage patterns.
What Are the Warning Signs of Truck Engine Problems?
You'll spot truck engine problems from signs such as unusual engine noise or reduced fuel economy. You may also notice unusual exhaust smoke, engine oil drips, or possibly a continuously lit check engine warning.
Is Technology Important for Truck and Fleet Maintenance Operations?
Technology is fundamental in optimizing truck maintenance. Telemetry systems deliver real-time data, while analytical tools forecast issues before they occur. You'll notice reduced downtime, better safety measures and as a result, cost savings. It's revolutionary.
Do Different Fleet Vehicles Have Unique Maintenance Requirements?
Different vehicle types certainly require specific maintenance schedules. One must account for the vehicle's purpose, load capacity, and driving conditions, as these factors significantly affect needed upkeep. Always adjust maintenance based on the vehicle category.
Conclusion
At the core, what matters most is ensuring your fleet operates efficiently, wouldn't you agree? Regular maintenance isn't just a suggestion, it's absolutely necessary. By pinpointing crucial elements, conducting routine checks, applying preventive maintenance approaches, and leveraging technological advances, you're not just maintaining your trucks, you're honing a well-oiled machine. And keep in mind, truck and fleet repair isn't a failure, it's a pathway to enhancement. Maintain your dedication, and you'll witness your fleet's check here performance, dependability, and durability soar to new peaks.